دستاوردها قابل توجه بوده اند. جهت گیری های آینده در ربع قرن پیش، اکنون تبدیل به مواردی مرسوم و کاربردهایی عادی از این فلز تطبیق پذیر اما گرانقیمت شده اند. تیتانیوم ریختگی (فصل 6 راببینید) قبل از اینکه یک روش تولید قابل قبول برای کاربردهای مربوط به قطعات هوافضایی حساس پدید آید به عنوان یک پیشرفت آتی برای بیش از یک دهه به حساب می آمد.
محدودیت های مربوط به پیشرفت های آتی: طراح یا کاربری که برای استفاده از تیتانیوم برنامه ریزی کرده است باید بداند که چه امکانی در این سیستم فلزی وجود دارد. مواد پیشرفته و فناوری های ذکر شده در این فصل، تا حد زیادی وضعیت فعلی خود را به پشتیبانی دولت ایالات متحده مدیون هستند. بسیاری از مفاهیم متالورژی تیتانیوم از جمله استفاده اولیه از این فلز در توربین های گازی نظامی و در هواپیمای مافوق صوت با پشتیبانی دولت ایالات متحده به ثمر نشست. هواپیمای جاسوسی مافوق صوت SR-71 نخستین استفاده از آلیاژ تیتانیوم بتا برای کاربردهای سازه ای هوافضا بود.
دانستن اینکه هزینه های توسعه ای بسیاری از فناوری های امروز را همانند گذشته به طور اختصاصی به وسیله بازار محدود صنعتی نمی توان در آغاز راه پشتیبانی نمود مسئله مهمی است. پشتیبانی دولتی (مانند ناسا و ارتش) برای توسعه و استفاده از فناوری های پیشرفته برای کاربرد بیشتر مفاهیم جدید لازم است اما برای موفقیت کافی نیست (با توجه به محدودیت بودجه دولت). البته، برخی مواد و فناوری ها ممکن است خطر فناورانه بسیار زیادی داشته باشند و در نتیجه، هزینه و احتمال خطر برای به کارگیری آنها مانع از سرمایه گذاری تجاری می شود. بنابراین، نکات جذابی که اکنون به طور محدود وجود دارند راه درازی برای باز کردن مسیر خود به سمت حوزه تجاری در پیش دارند.
شرکت های تولیدکننده اولیه تیتانیوم که هزینه تحقیق و توسعه زیادی را در پروژه های توسعه آلیاژ صرف کرده اند دارای اعتبار زیادی شده اند. کاربردهای تجاری تیتانیوم در بسیاری از موارد موجب توسعه نظامی شده اند. نیاز به توسعه توربین بخار و موارد مربوط به صنایع شمیایی، خوردورسازی، زیست پزشکی و ورزشی (علاوه بر دیگر موارد)، دلایل ثانویه ای بوده اند که به غنی سازی پایه فناورانه تیتانیوم کمک کرده اند. اما از دیدگاه واقع گرایانه، موادی نظیر کامپوزیت های زمینه فلزی یا فناوری هایی نظیر متالورژی پودر به دلیل الزامات نظامی توسعه یافته و خواهد یافت.
بحث پیشین درباره آلیاژهای پیشرفته و توسعه فرآیندهای مربوطه است. نباید چنین نتیجه گرفت که توسعه آلیاژهای مرسوم دچار رکود شده است. در صنعت زیست پزشکی، استفاده بیشتر از اندام های مصنوعی، تولیدکنندگان را نه تنها به تامین تیتانیوم خالص معمولی و Ti-6Al-4V بلکه به توسعه و/یا بازاریابی برای آلیاژهای جدیدتر نظیر Ti-6Al-7Nb و Ti-15Mo-3Nb تشویق کرده است.
تقاضا برای تیتانیوم در بازار زیست پزشکی در مدول کمتر آن (نسبت به آلیاژهای کبالت-کروم به کار رفته برای اندام های مصنوعی)، استحکام بالا و زیست سازگاری قابل توجه آن قرار دارد. کاربردهای مربوط به تیتانیوم و آلیاژهای آن از ایمپلنت های دندانی تا اندام های مصنوعی مربوط به ران و زانو تا ورق های استخوانی آرواره ای متغیر است. کاربردهای زیست پزشکی باید از رشد مستمر برخوردار باشند و نیز از به کارگیری قابلیت آلیاژهای دیگر نیز بهره مند باشند.
آلیاژهای پیشرفته تیتانیوم و فرآوری های مربوطه
همانطور که پیشتر ذکر شد، محدوده دمایی فعلی آلیاژهای کارشده و ریختگی تیتانیوم فرآوری شده حدود °C 595 (°F 1100) است. این محدوده عمدتا به دلیل مسائل مربوط به سطح طولانی و پایداری متالورژیکی بالک است هرچند استحکام خزشی به وضوح به طور پیوسته با دما کاهش می یابد. به منظور بهبود این محدوده تا °C 700 (°F 1290) و بالاتر، کامپوزیت های زمینه تیتانیومی و آلیاژهای دارای فاز بین فلزی تیتانیوم-آلومیناید ایجاد شده اند. دیگر کامپوزیت های پیشرفته از طریق استفاده از فناوری پیشرفته فرآوری متالورژی پودر با نرخ انجماد سریع (RSR) و آلیاژسازی مکانیکی مطالعه شده اند.
علاوه بر این پیشرفت ها در توسعه آلیاژ، دیگر جنبه های جذاب استفاده از تیتانیوم نیز در حال پدیدار شدن هستند. فرآروی افشانه ای پودر برای ایجاد پیش شکل، استفاده از شکل دهی سوپرپلاستیک و لایه نشانی بخار فیزیکی (PVD) برخی حوزه هایی هستند که نوید کاربردهایی نوین از تیتانیوم را می دهند.
آلومینایدهای تیتانیوم
با توجه به محدودیت های دمایی در آلیاژهای متداول تیتانیوم، سوپرآلیاژها در نواحی دمابالاتر توربین های گازی و دیگر سازه های هوافضایی مورد نیاز هستند. برای نمونه، جایگزینی سوپرآلیاژها در مراحل پایانی مقاطع داغ توربین گازی می تواند منجر به کاهش محسوس وزن شود. در توربین با فشار کم (LPT)، هرچه پیشرانه موتور افزایش می یابد، تیغه های توربین بزرگتر می شود که منجر می شود که دیسکی که تیغه ها را نگه می دارد و شافتی که با دیسک می چرخد، سنگین تر شوند. جایگزینی سوپرآلیاژهای پایه نیکل متداول با آلومینایدهای تیتانیوم، مشکل افزایش وزن این موتور را کم می کند. به دلایلی نظیر این، تحقیق و توسعه گسترده ای برای بیش از 3 دهه برای پاسخ به این پرسش انجام شده است: آیا ترکیبات بین فلزی آلومیناید تیتانیوم داکتیلی را می توان ساخت که با سوپرآلیاژهای پایه نیکل رقابت کنند؟
ترکیب های آلومیناید و خواص آنها
دسته های جدیدی از مواد بر پایه ترکیبات بین فلزی آلومیناید تیتانیوم ایجاد شده اند. در ابتدا دو کاندیدا برای ترکیب بین فلزی آلومیناید وجود داشتند: آلفا-2 (Ti3Al) و گاما (TiAl). پس از این دو ترکیب، ترکیب دیگری به نام بین فلزی اورتورومبیک بر پایه Ti2AlNb ایجاد شده است. این مواد اساسا دارای چگالی ای مشابه با تیتانیوم هستند اما می توان از آنها در دماهای بالاتر نیز استفاده کرد. آنها همچنین دارای دماهای ذوب و مدول های بالاتری هستند و مدول خود را با افزایش دما به طور بهتری حفظ می کنند. آلومینایدهای تیتانیوم دارای مدول های بالاتری در °C 816 (°F 1500) نسبت به مدول تیتانیوم در دمای اتاق هستند! آلومینایدها احتمالا حتی دارای حفظ استحکام بهتری در دماهای بالاتر نسبت به آلیاژهای تیتانیوم مرسوم موجود هستند.
آلومینایدها با تمایل به تشکیل TiO2 به جایAl2O3 با خواص محافظ بیشتر که مشخصه بیشتر سوپرآلیاژهای مقاوم به اکسیداسیون است شناخته می شوند. متعاقبا، آلومینایدها دارای مقاومت عالی ذاتی به اکسیداسیون در دماهای کمتر هستند اما یک تمایل محدودکننده به ورقه ورقه شدن پوسته های اکسیدی تشکیل شده روی این آلومینایدها در دماهایی بالاتر از °C 871 (° 1600) در حین تبرید وجود دارد. کلید افزایش دمای کاری بیشینه آلومینایدهای تیتانیوم، افزایش مقاومت به اکسیداسیون آنها در عین حفظ سطوحی کافی از حفظ استحکام و خزش در دماهای بالا می باشد. انتظار می رود دماهای کاری بالقوه برای آلومینایدهای تیتانیوم در حال حاضر از °C 600 تا 760 (°F 1400-1100) متغیر باشد.
دسته گاما از آلومینایدها دارای مقاومت به اکسیداسیون بیشتری نسبت به آلیاژهای آلفا-2 هستند. هرچند برای ایجاد آلیاژهایی برای افزایش بیشتر مقاومت به اکسیداسیون آلیاژهای گاما تلاش شد اما به نظر می رسد مزایای کلی همه انواع آلومینایدهای تیتانیوم در ایجاد پوشش های محافظ مناسب باشد. سه روش کلی ایجاد پوشش آلیاژی برای حفاظت آلومینایدهای تیتانیوم در نظر گرفته شده اند: آلومینایز کردن، پوشش های روی هم قرار گرفته فلز- کروم- آلومینیوم- ایتریم و سیلیسایدها/سرامیک ها. دو روش نخست، متناسب سازی ای از فناوری پوشش دهی توسعه یافته برای سوپرآلیاژها می باشند درحالی که روش آخر از فناوری مربوط به آلیاژهای فلزی دیرگداز برگرفته شده است. حفاظت از آلومینایدهای تیتانیوم در شرایط اکسیدکننده با هر سه روش حاصل شده است اما عمر خستگی ماده پوشش دهی شده غالبا کمتر از عمر خستگی ماده بدون پوشش است.
آلیاژهای آلفا-2 معمولا دارای 23 تا 25 درصد اتمی Al و 11 تا 18 درصد اتمی Nb می باشند. دیگر عناصر آلیاژی عبارتند از تا 3 درصد اتمی وانادیوم و 1 درصد اتمی مولیبدن. آلیاژهای گاما دارای 48 تا 54 درصد اتمی Al و 1 تا 10 درصد از یکی از عناصر زیر: وانادیوم، کروم، منگنر، نیوبیوم، تانتالیوم، تنگستن یا مولیبدن. اورتورومبیک ها معمولا دارای 21 تا 25 درصد اتمی آلومینیوم و 25 تا 30 درصد اتمی نیوبیوم می باشند.
آلومینایدها دارای داکتیلیته کمی در دماهای محیط می باشند هرچند داکتیلیته در دمای بالا معمولا رضایتبخش است. اما برای فرآروی و نصب برای کارکرد و تعمیر، داکتیلته کم در دمای محیط می تواند موجب مشکل شود. خزش و دیگر خواص دمابالا مناسب هستند هرچند در سالهای اولیه توسعه آلومینایدها، مطابق با انتظار نبودند.
شکل 14-1 مقایسه ای از رفتار خزشی آلیاژهای متداول تیتانیوم، آلفا-2 و آلومینایدهای تیتانیوم گاما ارائه می دهد. سطوح مورد انتظار از استحکام برای آلفا-2 و گاما در سالهای اولیه توسعه به ترتیب با سوپرآلیاژهای پایه نیکل اینکونل 713 و IN-100 قابل مقایسه بودند. این موارد اهداف جاه طلبانه ای بودند که به درستی تحقق نیافتند. برای کاربردهای دمابالای تا حدود °C 649 (°F 1200)، آلیاژهای تیتانیوم نیز به رقابت با آلیاژ استاندارد توربین گازی یعنی اینکونل 718 ممکن است امیدوار باشد. هرچند آلیاژهای آلفا-2 به حد کافی این استاندارد را برآورده نمی کنند اما آلیاژهای بین فلزی اورتورومبیک، نوید رسیدن به هدف یعنی اینکونل 718 را می دهند. شکل 14-2 برخی بین فلزی های تیتانیومی اورتورومبیک را با آلیاژ 718 و برخی آلیاژهای آلفا-2 مقایسه می کند.
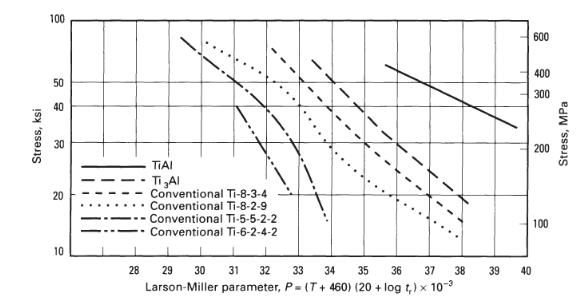
شکل 14-1 مقایسه رفتار خزشی آلومینایدهای تیتانیوم با آلیاژهای تیتانیوم معمولی
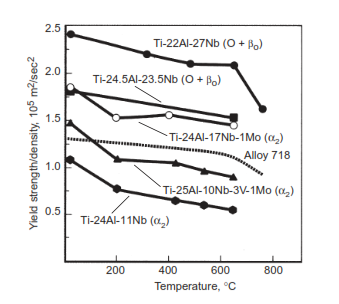
شکل 14-2 نسبت استحکام به وزن برای بین فلزی های اورتورومبیک و آلفا- 2 با سوپرآلیاژ اینکونل 718
برای استفاده کامل از قابلیتهای خواص مکانیکی آلومینایدهای آلفا-2 و گاما، ترکیب باید بهینه شود و کنترل میکروساختار نیز باید انجام شود. فرآوری ترمومکانیکی را برای کنترل مورفولوژی فازی و توزیع فاز در آلومینایدهای کارشده می توان استفاده کرد. آلیاژهای ریختگی به عملیات حرارتی مربوط به تنظیمات میکروساختاری تا یک ترکیب خاص متکی هستند.
فراوری و کاربرد
ذوب کردن، ریخته گری، فورج کاری، نورد کردن و اتصال دهی آلومینایدهای تیتانیوم به طور گسترده ای مطالعه شده اند. از دیگر فناوری های فرآوری نظیر ماشینکاری چشم پوشی نشده است. آلیاژها را می توان با روش های مرسوم از جمله ریخته گری، شمش ریزی و متالورژی پودر فرآوری نمود.
قطعات ریختگی ساخته شده به روش ریخته گری دقیق از آلیاژ پایه آلفا-2 ساخته شده و حلقه های مربوط به آستر احتراق با موفقیت از آن نورد شدند. در یک مورد، یک حلقه نوردشده درون یک محفظه چگالنده ساخته شد و به مدت 65 ساعت با موفقیت به کارکرد مشغول بود. دیگر قطعات مربوط به کاربرد دمابالا نیز ساخته و تست شده اند. در مقایسه با سوپرآلیاژ مرسومتر به کار رفته، صرفه جویی در وزن در یک کاربرد، به تنهایی 43 درصد بود.
با ظهور آلومینایدهای گاما از گروهی با ترکیب گسترده ای از بین فلزی های تیتانیوم، آلیاژ ریختگی Ti-48Al-2Cr-2Nb به طور گسترده ای برای استفاده در موتورهای توربین گازی تجاری ارزیابی شد. شکل 14-3 آلیاژ ریختگی را به شکل تیغه های توربین با فشار کم (LPT) برای موتورهای توربین گازی تجاری با پیشرانه بالا و ضریب گذر زیاد نشان می دهد. شکل 14-4 یک روتور با تیغه های LPT ریختگی از جنس Ti-48Al-2Cr-2Nb که به شکل بدون پوشش در °C 700 (°F 1292) در موتور شبیه ساز General Electric تست شده است را نشان می دهد.
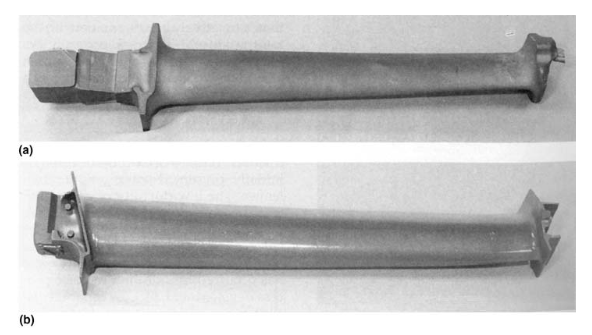
شکل 14-3 تیغه های آلومیناید گاما مربوط به توربین با فشار کم ساخته شده به روش ریخته گری مربوط به موتورهای توربین گازی General Electric.
الف- شکل خام مربوط به CFC-80C ب- تیغه اندازه شده برای GE90
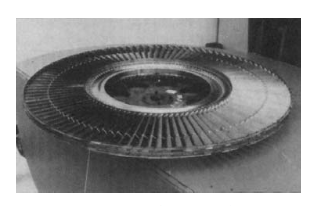
شکل 14-4 روتور توربین با فشار پائین با تیغه های آلیاژی ریختگی آلومیناید گاما پس از تست در توربین گازی General Electic
تولید سازه های ریختگی بزرگ به دلیل نیاز به پرس ایزواستاتیک داغ برای حصول خواص بهینه دشوار است. ادعا شده است که آلیاژ ریختگی Ti-48Al-2Cr-2Nb را می توان با فرآیند جوشکاری قوس با الکترود تحت پوش گاز و با جوشکاری پرتوی الکترون جوشکاری کرد. با ریخته گری سازه های بزرگ در بخشهای کوچک، پرس ایزواستاتیک داغ و جوشکاری ترمیمی آنها و سپس اتصال دهی بخش های کوچک با جوشکاری، نشان داده شده است که فناوری ریختگی آلومیناید را به بخش های حجیمتر توربین های گازی تجاری و نظامی می توان گسترش داد.
تعدادی از قطعات موتور توربین گازی به عنوان کاربردهای بالقوه مربوط به فناوری آلیاژ گاما تشریح شده در بالا شناسایی شده اند. این قطعات عبارتند از تیغه های توربین ثابت و چرخان در چگالنده های فشار بالا (HPC)، استاتورها، پره ها، محفظه ها، قطعات ثابت (نظیر محفظه های نفودی)، قطعات توربین (نظیر محفظه ها) و تیغه های LPT. کاربرد در خودرو برای آلومینایدهای تیتانیوم در قطعات ریختگی و کارشده انجام شده است. ادعا شده است که آلیاژهای گامای کارشده توازن بهتری از خواص مکانیکی با قابلیت فرآوری نشان می دهند.
آینده آلومینایدها
ممکن است این سوال پیش آید چرا مواد پایه آلومینایدی چندان مورد استفاده قرار نمی گیرند. پاسخ در تمایل کلی بسیاری از آلومینایدهای فلزی در همه انواع سیستمها به داشتن داکتیلیته محدود در دمای اتاق و چقرمگی شکست ضعیف قرار دارد. فرآوری و تولید قطعات سازه ای آلومینایدی به دلیل داکتیلیته و چقرمگی محدود در محدوده دمایی کمتر، دشوار است، بنابراین، به دمای بسیار بالای فرآوری نیاز دارند. این نقایص هنگامی که کار کردن روی آلومینایدها برای شکل دهی آنها به صورت محصول که به مقدار زیادی تغییرشکل نیاز دارند برجسته است. مثال های این مورد ورق مربوط به پنلها یا هسته های لانه زنبوری در هواپیما ویا سازه های هوافضایی می باشند.
ساخت ترکیب آلومینایدهای تیتانیوم، پرهزینه است. ادعا شده است کاهش هزینه برای آلیاژهای گامای به کار رفته برای قطعه ریختگی، هزینه پایه آلیاژ را تا محدوده آلیاژهای مرسوم کاهش می دهد. معلوم نیست که این کاهش هزینه ها جامه عمل به خود بپوشانند زیرا این موارد نه فقط به شکل یک پیشرفت فناورانه و گستره ای از الزامات مقررات بلکه در حجم استفاده پیش بینی شده اند. آلومینایدهای تیتانیوم هنوز هم بیانگر یک کاربرد فناورانه مورد تردید (از نظر خواص و فرآوری) هستند و احتمال استفاده گسترده از آنها در آینده نزدیک محتمل نیست.
کامپوزیت های زمینه تیتانیومی
مواد کامپوزیتی زمینه تیتانیومی (TMC) آلیاژهای تیتانیومی مرسومی هستند که با یک تقویتکننده از الیاف پیوسته تقویت شده اند. مفاهیم مواد کامپوزیتی نزدیک به چهار دهه است که با استفاده از زمینه های پلیمری و فلزی همراه با برخی موفقیتها مورد اکتشاف و استفاده قرار گرفته اند اما به طور خاص برای کامپوزیت های زمینه تیتانیومی اکتشافی صورت نگرفته است. سفتی و استحکام بسیار بالای الیافی که می توان در TMC به کار برد بدان معناست که کامپوزیت تیتانیومی می تواند سفتی ای به میزان تقریبی 2 برابر تیتانیوم معمولی داشته باشد که در واقع از سفتی فولاد بیشتر بوده و استحکامی نصف استحکام آلیاژ پایه تیتانیوم معمولی دارد.
فشار بیشتر برای عملکرد بهتر موتورهای هواپیما منجر به مطالعات توسعه ای روی مواد کامپوزیت زمینه تیتانیومی شده است. این مواد به عنوان یک گزینه آتی محتمل برای کاربردهای کلیدی به ویژه در توربین های گازی غیرنظامی محسوب می شوند. در طول اواسط دهه 1990، سه تولیدکننده اصلی توربین گازی (Pratt & Whitney, General Electric و Rolls Royce) تلاش های زیادی را برای کاهش قیمت و افزایش کیفیت و عملکرد مواد TMC در موتورهای توربین گازی آغاز کردند.
مواد TMC به الیاف های پیوسته محدود نیستند. الیافهای کوتاه و ویسکرها یا ذرات سرامیکی نیز برای استفاده به عنوان تقویتکننده در زمینه های تیتانیومی در نظر گرفته شده اند.
مواد کامپوزیتی زمینه تیتانیومی به طور کلی با تقویت کننده ای از نوع الیاف کوتاه از جنس کاربید سیلیسیم (SiC) تقویت می شوند. این مواد کامپوزیتی برای افزایش عملکرد دمابالای تیتانیوم و آلیاژهای آن ایجاد شده اند. مواد زمینه به کار رفته تا کنون عبارتند از Ti-6Al-4V، Ti-15V-3Sn-3Cr-3Al و Beta 21S (Ti-3Al-8V-6Cr-4Mo-4Zr). Beta 21S هنگامی که با SiC تقویت شود می تواند در برابر دماهایی تا حد °C 800 (°F 1500) ایستادگی نماید. الیاف کاربید سیلیسیم به طور کلی 35 تا 40 درصد حجمی کامپوزیت را تشکیل می دهد.
کامپوزیت های زمینه تیتانیومی تقویت شده با ذرات- به عنوان تقویت کننده ای ناپیوسته و گسسته- منبع دیگری برای استحکام بخشی به مواد کامپوزیتی هستند. این دسته از مواد شامل برخی افزودنی های سرامیکی یا بین فلزی (مانند TiC، TiB2 یا TiAl) در مقادیر بارگذاری مختلف (مانند 20-10 درصد وزنی) در یک زمینه آلیاژی تیتانیومی نظیر Ti-6Al-4V می باشد.
مواد آلومیناید تیتانیوم نیز در تلاش های پیوسته برای تولید مواد TMC به کار رفته اند. یک کاربرد از تقویت کننده ذره ای از تولید یک آلومیناید تیتانیوم گامای تقویت شده با 7 درصد وزنی ذرات TiB2 تشکیل می شود. این ذرات در زمینه با فرآیند بازذوب قوسی در خلاء برای تولید ترکیب آلیاژ گاما اعمال شدند. TMC ریخته گری شد، تحت پرس ایزواستاتیک داغ قرار گرفته و برای تولید قطعه تحت عملیات حرارتی قرار گرفت.
گزینه های فرآوری
هرچند در تولید مواد TMC سازگاری الیاف- زمینه و استحکام، داکتیلیته و ماندگاری حاصل همواره از اهمیت برخوردار است اما مانع اصلی در راه استفاده از این مواد، فرآوری ضروری برای تولید قطعات از TMC است. الیاف های کاربید سیلیسیم قادر به شکل دهی شدن به شکلی دوار با شعاعی دقیق نیستند. به علاوه، جابجایی رشته های الیاف عملی نیست. در نتیجه، مواد TMC تقویت شده با الیاف پیوسته در ساده ترین صورت، به شکل قطعاتی با هندسه نسبتا ساده تولید می شوند و در جایی به کار می روند که میدان تنش نیز نسبتا ساده باشد.
کلید عملکرد هر قطعه ساخته شده از ماده TMC، کنترل مناسب بر نقایص ساختاری ممکن است. ماده ای با 35 درصد حجمی فاز ثانویه نسبتا ترد دارای پتانسیل زیادی برای داشتن نقایص و عیوب است. الیاف ترک خورده و ترک های موضعی در زمینه مشکلات محتمل هستند. این مشکلات بوسیله فرآوری کنونی پوشش دهی الیاف با یک ماده زمینه تیتانیومی قبل از چیدمان و شکل دهی برطرف شده اند.
مواد کامپوزیتی غالبا به چیدمان آزمایشگاهی گسترده از نوارهای تولیدشده برای ایجاد ابعاد دلخواه قطعه نیازمند هستند. نوارها به عنوان راهی برای ایجاد توزیع پایدار از الیاف در زمینه مهم هستند. نوارها جابجایی و چیدمان را به شدت ساده می کنند.
برای استفاده از تقویت کننده های الیاف پیوسته، افشانش پلاسما یا لایه نشانی بخار فیزیکی بوسیله پرتوی الکترون برای لایه نشانی زمینه تیتانیومی روی الیاف به کار رفته است. الیاف را می توان به طور مستقیم برای چیدمان استفاده کرد یا اینکه برای تشکیل محصولی نواری با چگالی بالا با یکدیگر ترکیب نمود. فرآیندهای دیگری برای لایه نشانی پودر زمینه تیتانیومی دلخواه روی الیاف برای ایجاد یک محصول نواری موجود هستند. تعدادی از روش های فرآوری برای شکل دهی پیوسته کامپوزیت های تیتانیومی تقویت شده ارزیابی شده اند اما فقط اتصال دهی نوردی در دمای بالا و زمان کوتاه، پرس کاری ایزواستاتیک داغ و پرس کاری داغ در خلاء به طور عملی استفاده شده اند.
کامپوزیت های زمینه تیتانیومی تقویت شده با ذرات بوسیله فرآوری متالورژی پودر ساخته می شوتد. این مواد بوسیله پرسکاری ایزواستاتیک سرد تا شکل نزدیک به نهایی فرآوری می شوند و می توان آنها را با فورج کاری یا اکستروژن پیش شکل پودری به میزان بیشتری شکل دهی کرد. در مقایسه با آلیاژهای تیتانیومی که تقویت نشده اند، مواد تقویت شده با ذرات دارای استحکام کششی و مدول الاستیک بهتر در دمای اتاق و دمای بالا هستند و در نتیجه، دمای استفاده را در تقریبا همان چگالی افزایش می دهند.
آینده کامپوزیت های زمینه تیتانیومی
پژوهش جالبی روی مواد TMC انجام شده و بیشتر این تلاشها بوسیله دولت و صنعت از نظر مالی پشتیبانی شده و می شوند. قطعه تقویت شده با ذره نشان داده شده در شکل 14-5 دارای شواهدی موثر از آنچه ممکن است انجام شود می باشد. قطعه TMC دارای نصف چگالی قطعه ضدزنگی بود که جایگزین آن شد و در دماهای عملکردی، استحکام بیشتری داشت. هرچند دو ماده پیشرفته (آلومینایدها و کامپوزیت ها) به کار رفتند اما کاربرد مکرر نظامی یا حتی تجاری از اینها، یک امکان کوتاه مدت نیست.
هزینه TMC با هزینه الیاف و نیز هزینه شکل دهی چیدمان قطعه واقعی به شدت تحت تاثیر قرار می گیرد. هزینه های الیاف به دلیل حجم نسبتا کم بالاست. کاهش هزینه الیاف ممکن است اما باید هزینه پوشش دهی الیاف و تولید نوار را نیز در نظر گرفت. هزینه تولید، پایداری خواص محصول، مقاومت به اکسیداسیون الیاف و زمینه و قابلیت ترمیم، از چالش های عمده در کاربرد مواد TMC می باشند. این امر نامحتمل است که این مواد برای کاربردهای تجاری استاندارد برای سالهای پیش رو مفید باشند و ممکن است هیچگاه، این مواد به جایگزین هایی مقرون به صرفه برای قطعات فلزی تبدیل نشوند.
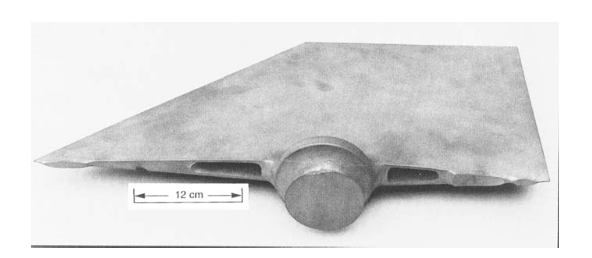
شکل 14-5 بال موشک از جنس تقویت شده با ذره آلومیناید در قطعه تولید شده به روش ریخته گری دقیق و HIP شده و عملیات حرارتی شده
دیگر روش های فرآوری
شکل دهی سوپرپلاستیک/ اتصال دهی نفوذی (SPFDB) به طور مختصر در فصل 9 تشریح شد. برای طراحی هایی که از قطعات ورقی تقویت شده از نوع لانه زنبوری یا موارد مشابه استفاده می کنند، ترکیب کردن شکل دهی و اتصال دهی بوسیله روش SPFDB، تبدیل به یک روش تولید مناسب شده است.
درون سازه هایی که با گاز تحت فشار می توان به آنها دسترسی داشت از نظر مفهومی همانهایی هستند که برای ایجاد یک ساختار پیچیده شامل دندانه ها، دابلرها یا دیگر تقویت کننده ها لازم می باشند. طراحان باید ملاحظاتی جدی را در کاربرد روش های SPFDB در ساخت قطعات جدید به کار گیرند. این حقیقت که تولیدکنندگان بزرگ موتور هواپیما از SPFDB برای تولید قطعات دوار حساس نظیر تیغه های توخالی پره ها برای توربین های گازی بزرگ استفاده می کنند نشان می دهد که این فناوری برای تقریبا هر نوع کاربرد به کارگیرنده ترکیب هایی از آلیاژ تیتانیوم قابل قبول است. البته بسته به اینکه میزان حساسیت قطعه در کاربرد چه مقدار است هزینه می تواند باز هم یک مسئله باشد. سازه های بزرگ به کوره های بزرگ نیاز دارند و جنبه اتصال دهی نفوذی فرآیند به طور حساسی به تمیزی و چیدمان قطعات بستگی دارد.
شکل دهی افشانه ای و شکل دهی لیزری
یکی از مهمترین ملاحظات در تولید قطعات از تیتانیوم به روش متالورژی پودر، مقدار اکسیژن است. فرآوری نزدیک به شکل نهایی بوسیله روشهای پودری همچنان در آلیاژهای تیتانیوم یک هدف گذاری محسوب می شود. روشهای مختلف شکل دهی افشانه ای به عنوان روشهایی برای تولید یک شکل معین به طور مستقیم و بدون نیاز به قالب یا قوطی نظیر روشهای به کار رفته در پرسکاری ایزواستاتیک داغ، دارای پیشرفت بوده اند. در اینجا قطعه بوسیله لایه نشانی پیوسته پی درپی پودر با افشاندن ساخته می شود. روشهای افشاندن شامل افشاندن گرمایی، فرایند Ospray و افشاندن پلاسمایی در فشار کم می شوند. علی رغم بهترین اقدامات پیش گیرانه، این فرآیندها معمولا از اکسیژن مکمل استفاده می کنند که به شدت بر خواص قطعه افشانده شده تاثیر می گذارد.
شکل دهی افشانه ای حالت جامد (SSF) به عنوان روش دیگری به جز روشهای پیشتر ملاحظه شده به کار رفته است. فرآیند SSF از پودر تیتانیوم بدون اکسیژن تولید شده با فرآیند هیدرید- دی هیدرید (HDH) استفاده کرد و یک عملیات لایه نشانی در دمای کم است. ماهیت فرآیند SSF، استفاده از پودرهای خاص تولیدشده از HDH و برخوردهای با سرعت بالای این ذرات پودر با شتاب دهنده SSF می باشد. نتیجه این عملیات، ایجاد اتصال دهی آنی در حالت جامد است. کار اولیه روی SSF (با پودرهایی که عاری از اکسیژن نیستند) به آنیل کاری بعدی و پرسکاری ایزواستاتیک گرم برای تکمیل فرآیندهای تولید قطعه نیاز داشت.
فرآیندهای افشاندن قابلیت چشمگیری دارند اما بعید است که مقرون به صرفه باشند. هزینه پودر، موردی قابل توجه در فرآیند تولید است. به علاوه، تولید شکل های غیرمتقارن را می توان با سطح یکسان از خواص در کل قطعه، همانند آنچه در قطعات متقارن رخ می دهد قطعی نیست. فرآیندهای دیگری مربوط به SSF نیز گزارش شده اند. روش افشاندن گاز سرد (CGSM) عملکرد خوبی در لایه نشانی پوشش ها در دمای پائین یا ساخت بیلت هایی از آلیاژهای تیتانیوم داشته است. همچنین، ادعا شده است که CGSM مزایایی برای سلامتی، ایمنی و جنبه های زیست محیطی در مقایسه با فرآیندهای سنتی افشانش دارد. نشان داده شده است که CGSM را می توان برای اثرات ترمیمی بر قطعات تیتانیومی بدون ایجاد آسیب به ماده زیرلایه به کار برد. علی رغم تقاضا برای این فرآیندهای دما پائین، این احتمال وجود دارد که جنبه های اقتصادی افشاندن پودر، چنین فرآیندهایی را در تولید قطعات تیتانیومی به فرآیندهایی با اثرگذاری محدود تبدیل کند.
یکی از فرآیند مربوطه، شکل دهی لیزری قطعات تیتانیومی است که ادعا شده است که زمان لازم برای تولید سازه های پیچیده تیتانیومی را 50 تا 75 درصد کاهش می دهد. Lasform عنوانی است که برای فرایند لایه نشانی مستقیم فلز به کار می رود. در این فرآیند، روکش کاری لیزری با توان بالا با روشهای پیش نمونه سازی پیشرفته سریع ترکیب می شود تا قطعات سه بعدی مستقیما تولید شوند. این روش به روشهای پیش نمونه سازی سریع نظیر استریولیتوگرافی و تفجوشی لیزری انتخابی شبیه است. اما انجام این کار در یک قطعه با چگالی کامل و پیوستگی و عدم نقص زیاد بدون استفاده از مراحل فراوان میانی نظیر ریخته گری یا پرس کاری ایزواستاتیک گرم انجام می شود.
لیزر انرژی لازم را برای انتقال پودر آلیاژی تیتانیوم منتخب به شکلی که در آنجا لایه نشانی می شود تامین می کند. این فرآیند در یک گاز خنثی بدون حضور اکسیژن زیاد انجام می شود. فرآیند Lasform- همانند همه فراوری های شکل نهایی- مراحل ماشینکاری و ضایعات ماده را کاهش می دهد. خواص یک آلیاژ Ti-6Al-4V Lasform شده در جدول 14-1 نشان داده شده است. یک پیشنهاد چشمگیر برای شکل دهی لیزری، لایه نشانی انتخابی ترکیبات آلیاژی مختلف برای بهینه سازی خواص مکانیکی در نقاط خاصی روی یک قطعه است. نظرات مربوط به دیگر فرآیندهای شکل دهی افشانشی پودر در اینجا نیز کاربرد دارند. نشان دادن اینکه خواص مکانیکی، متناظر با آلیاژهای تیتانیومی فورج شده یا حتی ریختگی هستند دشوار است و هزینه پودر و فرآیندهای افشانش و پساافشانش برای غیرقابل پذیرش کردن چنین فرآیندهایی برای کاربردهای تجاری، قابل ملاحظه است.
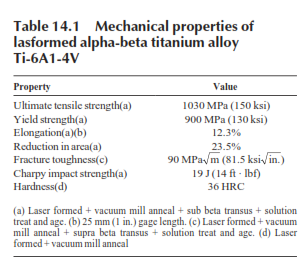
جدول 14-1 خواص مکانیکی آلیاژ تیتانیوم lasform شده آلفا- بتای Ti-6Al-4V
فناوری نانوساختار و فرآوری انجماد با نرخ سریع
مواد نانوساختار موادی هستند که دست کم یک بعد آنها در محدوده نانوساختار باشد. این بدان معناست که یک بعد کمتر از nm 100 داشته باشند (برخی نویسندگان مقادیر کمتری پیشنهاد داده اند). برخی علاقه مندان به تیتانیوم، از استفاده از فرآوری نانوساختار به عنوان راهی جدید برای گسترش قابلیت های آلیاژهای تیتانیوم دفاع کرده اند. تحقیقات درباره آلیاژهای تیتانیوم شامل استفاده از آلیاژسازی مکانیکی و نیز دیگر روشها می شود.
در افزایش قابلیت ساختارهای بینهایت ریز مواد نانوساختار، پیشرفت زیادی در زمینه ظرفیت داکتیلیته و تغییرشکل پلاستیک تیتانیوم انجام شده است و به طور کلی، خواص تیتانیوم در دمای کمتر مسئله بزرگی در کاربرد تیتانیوم به حساب نیامده است. محدوده دمای بالا همان چیزی است که نیاز به گسترش دارد و آلیاژهای ریزدانه نانوساختار احتمالا تقاضا درباره مقاومت بهتر به خزش در دمای بالا را برآورده نمی کنند.
فرآوری انجماد با نرخ سریع (RSR) یک دسته جداگانه از مواد نانوساختار است اما مربوط به ساختارهایی می شود که نمی توان با فناوری متداول به تولید آنها پرداخت. به طور خاص، عقیده بر آن است که تولید آلیاژهای مفید استحکام یافته با پراکندگی ذرات ریز با RSR احتمالا ممکن است.
استحکام بخشی با پراکنده سازی با ذرات ریز عبارتست از تولید موادی خاص به ویژه با رسوب درجای ذرات در زمینه یک آلیاژ. سوپرآلیاژهای پایه نیکلی و آلیاژهای آلومینیومی سیستمهای پایه ای هستند که به رسوب یک ذره فاز ثانویه برای افزایش شدید استحکام بستگی دارند. معمولا، عناصری به آلیاژ مذاب در فرایند شمش ریزی افزوده می شوند و در مرحله ای دیگر در فرآوری، این عناصر حل شده (یک عملیات حرارتی انحلالی) و باز رسوب پیدا می کنند (فرایند پیرسازی) تا ذرات ریزی از یک فاز ثانویه پراکنده شده در زمینه ایجاد کنند.
ذرات پراکنده شده را می توان با به کارگیری ذارت جامد یا ایجاد چنین ذراتی در حین فرایند ذوب به جای رسوب تولید کرد. ذرات ریز اکسید یا سیلیسایدی در میان مواردی هستند که در سیستمهای فلزی به کار رفته اند. این ذرات برخلاف روشهای درجا، در افزایش استحکام موثر نیستند اما مزایای آنها در دماهای بالا دوام بیشتری دارند.
استحکام دهی با ذرات ریز به شدت می تواند به هدف افزایش ظرفیت دمایی تیتانیوم کمک کند. هرچند بهبود در قابلیت استحکام دمابالا، هدف تصریح شده از ذرات ریز در سیستمهای پایه تیتانیومی می باشد اما اگر بتوان ذرات ریز مرسوم را با فرایندهای رسوب سازی تولید کرد بهبود در ویژگی مذکور می تواند در کل محدوده دمایی رخ دهد. دستیابی به ذرات ریز مرسوم در آلیاژهای پایه تیتانیومی دشوار است هرچند سیلیسیم در بهبود قابلیت دمابالای سیستمهای مرسوم مفید بوده است. بیشتر آلیاژهای تیتانیوم مرسوم مربوط به کاربرد در دمای بالا دارای سیلیسیم افزوده شده (مانند Ti-6Al-2Sn-4Zr-2Mo+Si) برای ایجاد استحکام دهی از طریق ذرات ریز با افزودن 0.25 تا 0.5 درصد سیلیسیم هستند.
متاسفانه، رسوب ذرات ریز درجا در فرایند شمش ریزی معمولی منجر به نتیجه رضایت بخشی نشده است. حفظ عناصر رسوب زای بالقوه در محلول فوق اشباع در تیتانیوم با تبرید بی نهایت سریع احتمالا ممکن است. RSR شامل روش های مختلفی برای تبرید بسیار سریع آلیاژهای تیتانیوم مذاب است. با استفاده از این روشها، عناصر دلخواه آلیاژی ای که در انجماد سریع حتی با اتمیزه کردن در فرایند الکترود دوار پس زده می شوند، در محلول حفظ می شوند. در نتیجه، آنها می توانند در مراحل بعدی فرآوری، به شیوه ای مطلوب پراکنده شوند و ذرات ریز ایجاد کنند.
روشهای RSR از طریق تشکیل پودرهای تیتانیوم برای فرآوری در قطعات قابل استفاده به کار رفته اند. پودر حاصل از RSR در حال حاضر محدود به یک بعد است تا خروج گرما تسهیل شود. این حقیقت بدان معناست که RSR، بسط یافته از فناوری متالورژی پودر است و انجام این فرایند، نسبتا پرهزینه است. برای توجیه انجام این فرایند، بهبود محسوسی در خواص آلیاژ باید رخ دهد.
فرآوری RSR برای به کارگیری درصدهای بالا از ترکیبات متالوئیدها (کربن، بور، سیلیسیم، گالیوم) به کار رفته است. عناصر نادر خاکی (RE) نیز افزوده شده اند اما آنها بیشتر برای اکسیژن زدایی (که از فرایند ساخت پودر موجود است) به کار می روند تا تولید رسوبات RE با تیتانیوم. اکسیدهای RE تشکیل شده اند و برای ایجاد سختی با ذرات ریز مناسب هستند. در آلیاژهای RSR فرآوری شده با بور، یک فاز بورید تیتانیوم رسوب می کند. هرچند آلیاژهای تیتانیوم آلفای مرسوم را می تواند با رسوب سازی ناشی از RSR، دچار استحکام سازی ناشی از ذرات ریز کرد اما ادعا شده است که بیشترین مزایا از آلیاژهای با طراحی خاص حاصل خواهد شد.
توزیع ذرات ریز باید به طور منطقی در دمای کارکرد یک سیستم پایدار باشد به طوری که معیار بهبود سیستمهای پایه تیتانیومی، صرفا ایجاد توزیعی از ذرات ریز نیست بلکه ایجاد یک توزیع پایدار از ذرات ریز برای کاربرد در بالاتر از تقریبا °C 700 (°C 1290) است. RSR یک فرایند با هزینه بالاست و هزینه استفاده از آن توجیه نشده است. نه تنها پس از چند دهه استفاده، آلیاژهای قابل توجهی حاصل نشده اند بلکه این نگرانی نیز وجود دارد که حفظ تاثیرات پراکنده سازی ذرات ریز برای ایجاد آلیاژهای خوب در دماهای بالا ممکن نباشد. هرچند ممکن است برخی کاربردها از RSR در تیتانیوم در آینده وجود داشته باشد اما RSR برای ایفای نقش محسوسی در گسترش محدوده دمایی این فلز، نامحتمل به نظر می رسد.
آلیاژهای تیتانیوم دما بالاتر مرسوم
کاربرد آلیاژهای تیتانیوم مرسوم در دماهای بالاتر برای سالیان بسیار مطالعه شده است. دمای عملکردی آلیاژهای تیتانیوم نسبت به نقطه ذوب فلز پایه کاملا پائین است. اگر بتوان این دما را به کسری مشابه با سوپرآلیاژهای پایه نیکلی افزایش داد، تغییرات زیادی را در طراحی را می توان احتمالا بدست آورد (توجه کنید که پایداری سطحی و مقاومت به تردی با انباشت اکسیژن را باید در نظر داشت).
چهار دهه پیش، ادعاهای زیادی درباره استحکام در برابر گسیختگی ناشی از خزش آلیاژهای شبه آلفا یا سوپرآلفا نظیر Ti-5Al-5Sn-5Zr با مقاومت به خزش بسیار بهتر نسبت به آلیاژ بسیار پرکاربرد Ti-6Al-4V وجود داشت. یکی از دلایلی که آلیاژهای سوپرآلفای اولیه نظیر Ti-5Al-5Sn-5Zr موفق نبودند این بود که به نظر می رسید چنین آلیاژهایی به ترک خوردگی در اثر خوردگی همراه با تنش (HSSCC) در نمک داغ حساس تر بودند که در زمان خود، یک چالش در طراحی محسوب می شد. بعدها، بکارگیری ترکیبات آلفا- بتای تیتانیومی جدید، مقاومت به خزش را با ایجاد تمایل اندک به وقوع HSSCC بهبود داد. ظاهر Ti-6Al-2Sn-4Zr-2Mo و افزودن مقادیر اندکی سیلیسیم (0.25 درصد) به طور محسوسی ظرفیت خزشی را بهبود داد. فرآوری بتا نیز برای بهبود مقاومت به خزش بکار برده شد.
در طول سالیان گذشته، تلاش محسوس بیشتری برای افزایش ظرفیت دمایی آلیاژهای مرسوم بکار برده شد. برای چنین آلیاژهایی، پیشرفت های نهایی در حال حاضر در IMI 834 و Ti 1100 متبلور شده اند که هردوی آنها در دماهایی کمی بالاتر از آلیاژهای متداول پیشین خود یعنی حدود °C 595 (°F 1100) در مقایسه با °C 566 (°F 1050) برای آلیاژهایی نظیر Ti-6Al-2Sn-4Zr-2Mo+Si قابل استفاده هستند.
حتی اگر آلیاژهای متداول جدیدی را با ظرفیت خزش بالاتر از آلیاژهای کنونی بتوان ایجاد کرد، هیچ نشانی برای افزایش مقاومت به انباشت اکسیژن و بهبود پایداری متالورژیکی وجود ندارد. اما این شرط همچنان باقی است که در آن، محدودیت های محیطی و قرارگیری در معرض محیط، نقطه بالایی دمایی را برای کاربرد آلیاژهای متداول تیتانیوم محدود می نماید. یک راه حل برای مسئله پایداری سطحی می تواند بکارگیری پوشش ها باشد اما حتی در این مورد نیز اثر ناچیزی از بهبود در آینده نزدیک وجود دارد.
نتیجه گیری ها
آلیاژهایی با هزینه کم
برای بیش از یک دهه، صنعت تیتانیوم با توسعه آلیاژها و فرایندهایی که به طور خاص برای کاستن از هزینه های کاربرد تیتانیوم مورد بررسی قرار گرفته است. در اوایل دهه 1990، مجموعه ای از آلیاژهای تیتانیوم (جدول 14-2 را ببینید) به کار رفت که ادعا شد که موجب کاهش قیمت بدون کاستن محسوس از خواص شدند. این هزینههای کمتر از طریق اصلاحاتی در عملیات های ذوب قوسی و در مراحل بعدی تولید به دست آمدند. استفاده از قراضه ها در یک مورد افزایش یافت و جایگزینی عنصر آلیاژی انجام گردید. آلیاژ Ti-6Al-1.7Fe-0.1Si با ادعایی مبنی براینکه خواص مکانیکی آن با آلیاژ Ti-6Al-4V قابل مقایسه بودند به کار برده شد. اما آلیاژ Ti-6Al-4V همچنان موقعیت خود را به عنوان آلیاژ تیتانیوم غالب در کاربردهای تجاری و نظامی حفظ کرده است.
آلیاژهای با هزینه کمتر همانند آلیاژهای جدید، به دلیل هزینه های مربوط به ایجاد یک پایگاه داده ای جدید برای خواص آنها، برای جایگزینی آلیاژهای موجود با دشواری در زمان مواجه هستند. به طور کلی مجسم کردن آلیاژی با داده های کششی در دمای اتاق که قابل مقایسه با آلیاژ دیگر باشد مطلوب است. ایجاد داده هایی جامع که برای همه آلیاژهای جدید قابل اعمال باشد برای یک طراح در استفاده از یک آلیاژ جدید احساس راحتی ایجاد می نماید.
با تجدید حیات صنعت تیتانیوم در اواسط تا اواخر دهه گذشته، نیاز فوری به کاهش هزینه برای تشویق استفاده از تیتانیوم بدلیل فضای فوق العاده تجاری شاید تعدیل شده باشد. پاسخ به این پرسش که آیا آلیاژهای با هزینه کمتر در آینده استفاده خواهند شد یا خیر تا حدی بوسیله ظرفیت تولیدکننده (یا فرا ظرفیت تولیدکننده) برای ساخت اسفنج و نیز محدوده ای که در آن تولیدکنندگان و کاربران، به صرف منابع برای ایجاد داده های طراحی علاقه دارند تعیین خواهد شد. کاربردهای مربوط به موقعیتهایی با قابلیت کمتر در به خطر افتادن زندگی (مانند صنعت خودرو) دارای شانس مناسبی برای تطبیق یاقتن با آلیاژهای تیتانیوم با هزینه کمتر هستند.
فرایندهای تجاری ادغام، شکلدهی و تثبیت
شاید یکی از تغییرات محسوس تر رخ داده در صنایع تیتانیوم (و دیگر صنایع)، روند شکل دهی و تثبیت مقررات باشد. این لزوما به معنای داشتن آلیاژی کمتر نیست بلکه بدان معناست که یک آلیاژ با مقررات کمتری کنترل خواهد شد. بر اساس توافقات برای استفاده از استانداردهای متداول تر در صنعت، مشتریان موجب می شوند که تولیدکنندگان و فراوران (مانند فورج کننده ها و ریخته گران) از قیمت های خود بکاهند و در نتیجه، هزینه های مشتریان نیز کاسته خواهد شد. در حالی که این موضوع یک کار تجاری مناسب است اما باید دید که آیا از نظر فنی نیز مناسب است یا خیر. البته سطح خواص با شکل دهی و تثبیت مقررات بهبود نخواهد یافت.
روزنه های جدید
روزنه های مختلفی برای تیتانیوم و آلیاژهای آن وجود دارد که به افزایش خود ادامه خواهند داد اما نرخ این افزایش همانند نرخ غیرقابل باوری که تیتانیوم در حوزه گلف پذیرفته گردید (و سپس تا حد زیادی جایگزین شد) نخواهد بود. پیش بینی روندهای کاربرد در این مورد همواره دشوار است و صنعت تیتانیوم در طول بیش از نیم قرن وجود تجاری خود، دارای فراز و نشیب های فراوانی بوده است.
کاربرد چشمگیری که در 1999 اعلام شد، ساخت برنامه ریزی شده قایق ماهیگیری تمام تیتانیومی در ژاپن بود. مطابق با این پیشرفت، کشتی تمام تیتانیومی موجب بازدهی محسوس سوخت، هزینه های نگهداری کمتر و سرعت بیشتر است. برنامه هایی نیز برای تولید آتی قایق های تفریحی، کشتی های خصوصی، قایق های سریع السیر پلیس و نیز درصورت موفقیت قایق تمام تیتانیومی، قایق های ماهیگیری دیگر اعلام شده است. شاید کشتی های تمام تیتانیومی یک موفقیت اقتصادی باشند و موجب روزنه جدید تجاری برای این فلز شوند.
خودروی تمام تیتانیومی نیز قریب الوقوع است اما بدون تردید، استفاده فزاینده ای برای این فلز در کاربردهای خودرویی وجود خواهد داشت.
تیتانیوم مقاوم در برابر سوختن
دیگر جنبه جالب فناوری تیتانیوم چالش مربوط به تولید یک آلیاژ تیتانیومی است که تمام مقاطع در روتور چگالنده تمام تیتانیومی را در توربین های گازی، ایمن تر کند. در روتورها، سایش یا وجود نقایص در قطعات چسبیده به هم می تواند موجب برخورد تیغه ها (اجزای دوار) به پره های استاتور (اجزای غیردوار) شود. گرمایش اصطکاکی می تواند به سرعت موجب وقوع یک آتش مهیب شود. در طراحی کنونی، ملاحظات مربوطه، از کاربرد روتورهای تیتانیومی در نزدیکی پره های استاتور تیتانیومی در یک توربین گازی با چگالنده ای با فشار بالا (HPC) جلوگیری می کنند.
قطعاتی از آلیاژ تیتانیوم با مقطع نازک در هنگامی که با یک منبع گرمایی قوی نظیر گرمای حاصل از ساییده شدن شدید تیغه ها و پره های استاتور دچار احتراق شوند در هوا ممکن است بسوزند. ترمودینامیک اکسیداسیون سریع تیتانیوم به معنای احتراق بسیار شدید است اگر در حضور آلیاژهای متداول تیتانیوم، آتشی آغاز شود. افزایش مقاومت به سوختن آلیاژهای تیتانیوم موجب کاربرد گسترده تر خواهد شد و منجر به کاهش وزن تقریبا 50 درصدی (برای هر قطعه) با استفاده از آلیاژهای تیتانیوم برای جایگزینی فولادها و سوپرآلیاژهای پایه نیکلی کنونی می شود.
در دهه 1990، چندین برنامه برای توسعه آلیاژهای تیتانومی مقاوم به سوختن در حال اجرا بودند. یک آلیاژ بتای مقاوم در برابر سوختگی یعنی Alloy C (Ti-35V-15Cr) بوسیله Pratt & Whitney با همکاری Wah Chang برای استفاده در موتور توربین گازی F119 توسعه یافت. تست های سوختگی مطابق با شکل 14-6 به نتایجی منجر شد که از آن مشخص است که Alloy C موجب مزیت دمایی قابل توجه نسبت به Ti-6Al-4V می شود. در انگلستان برای ایجاد یک آلیاژ از نظر قیمتی رقیب برای Alloy C پژوهش صورت گرفته است. این موضوع محتمل است که این آلیاژها کاربردهای نظامی قابل توجهی پیدا کنند اما ملاحظات ایمنی برای طراحی موتور توربین گازی تجاری موجب تردید در به کارگیری تیتانیوم مقاوم در برابر سوختن خواهد شد.
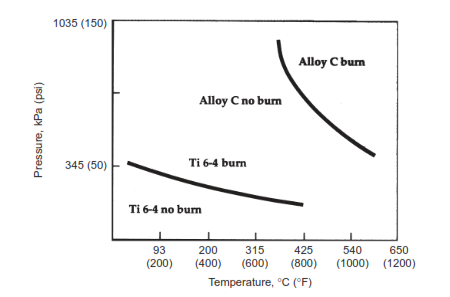
شکل 14-6 موقعیت نواحی مقاوم به سوختگی و غیرمقاوم به سوختگی مربوط به آلیاژ C و آلیاژ تیتانیوم آلفا- بتای Ti-6Al-4V
وضعیت موجود در توسعه آلیاژ
موج ادغام ها و تغییر مالکیتها در انتهای دهه 1990، نشان دهنده تغییرات زیاد در فضای کسب و کار بود. آلیاژهای جدید حاصل کار تولیدکنندگانی با نظم و قاعده همیشگی نیستند. در واقع، همه آلیاژهای جدیدا به کار رفته پیش از 1990 ابداع شده اند. آلیاژ Ti-6Al-4V، پس از حدود نیم قرن هنوز هم پرکاربردترین ترکیب است. تولیدکنندگان ابزارهای ورزشی (مانند چوب گلف و دوچرخه) همگی از آلیاژهایی بادوام برای محصولات خود استفاده می کنند.
به جز حوزه های معین، هر شخص مشتاق به بکارگیری آلیاژهای تیتانیوم در یک محصول، با آلیاژهای جدید معدودی برای انتخاب در دهه آینده مواجه خواهد بود هرچند که آلیاژهایی با قیمت کمتر بیشتر در دسترس خواهند بود. عدم ایجاد آلیاژ جدید شاید چیز بدی هم نباشد زیرا آلیاژهای کنونی حتی دارای پیشینه طولانی تری از کاربرد موفق خواهند بود.
قابلیت رشد
بزرگترین حوزه رشد برای تیتانیوم در آینده نزدیک، بدون تردید افزایش مستمر در کاربرد قطعات ریختگی برای محصولات تجاری خواهد بود. تولید قطعاتی نزدیک به شکل نهایی، هزینه محصولات تیتانیومی را کاهش خواهد داد و ریخته گری یک فناوری ثابت شده برای تولید چنین قطعاتی است. استفاده گسترش یافته از قراضه تیتانیوم محتمل است و آزادسازی و تثبیت مقررات به کاهش بیشتر هزینه ها بوسیله تولیدکنندگان باید کمک نماید.
پایان فصل چهاردهم و پایان کتاب